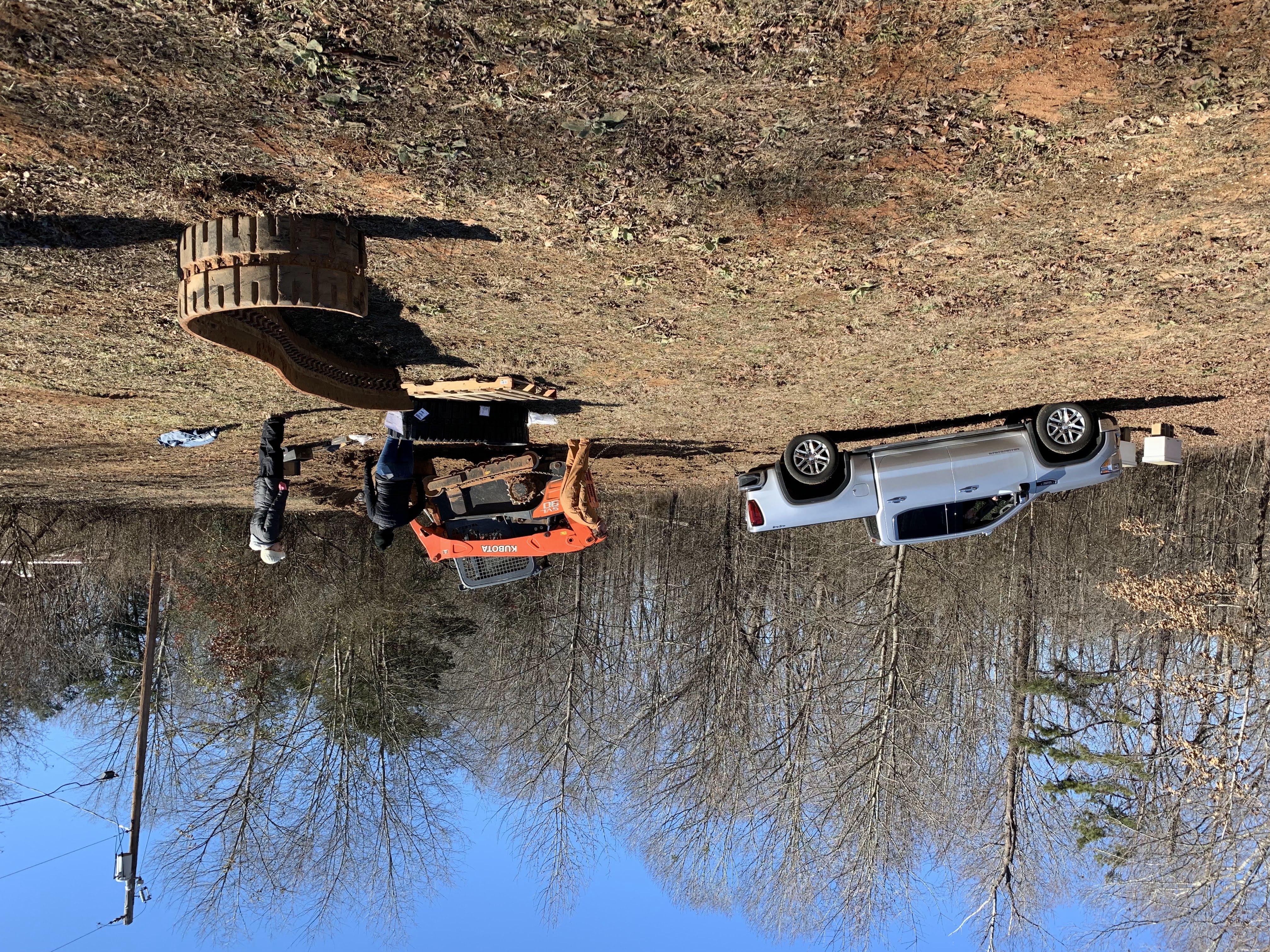
Farm projects
Kubota SVL-90 Track Replacement
It was a family affair replacing the track on the skidsteer.
read moreFarm projects
It was a family affair replacing the track on the skidsteer.
read more2021 texas
2021 texas
The Lord’s Chicken Sauce
read more2021 texas
2021 texas
Brooke’s best picture time
read more2021 texas
Leaving Elle OMG Buc-ees is a thing.
read more2021 texas
The flies were crazy because of all the rain
read more2021 texas
Yay for an old lunch tray!
read more